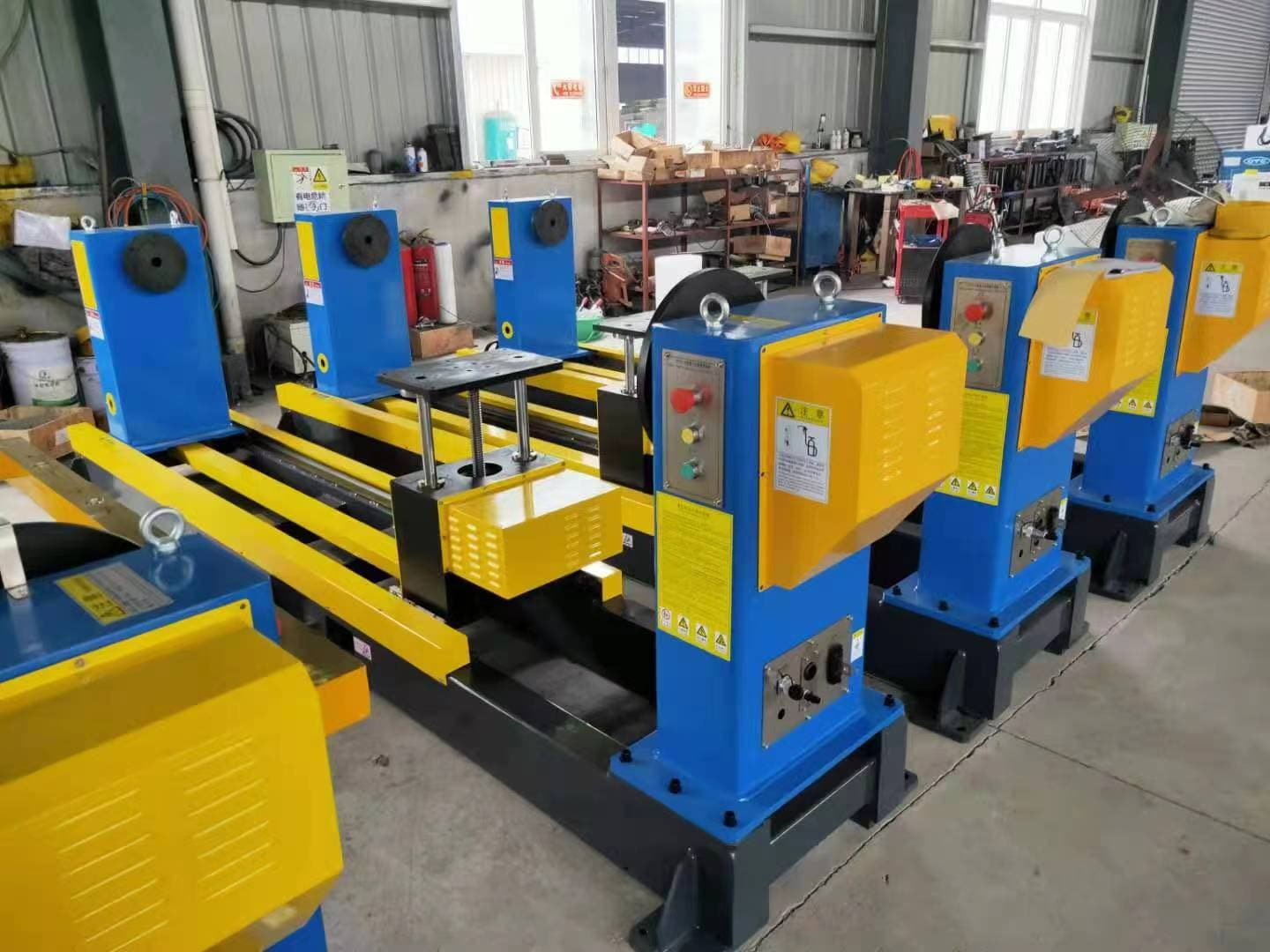


Head and Tail Box Moved Type Single-Axis Robot Servo Welding Positioner – Precision Automation for ABB, KUKA, FANUC Integration
Product Description
The Head and Tail Box Moved Type Single-Axis Robot Servo Welding Positioner revolutionizes robotic welding workflows by combining precision, flexibility, and industrial-grade durability. Engineered for seamless integration with ABB, KUKA, FANUC, and other leading robot brands, this positioner features synchronized head and tail box movement along a single axis, enabling optimal workpiece alignment for complex welding tasks. Ideal for automotive, aerospace, and heavy machinery applications, it ensures flawless weld quality while reducing setup time and operational costs. Built to withstand harsh industrial environments, it’s the ultimate solution for high-volume production and intricate welding projects.
Key Features
Single-Axis Servo Control: Precision movement of head and tail boxes for accurate workpiece positioning.
Adjustable Head & Tail Units: Independently adjustable clamps to accommodate varying workpiece lengths and geometries.
High Load Capacity: Supports workpieces up to [X] kg for heavy-duty welding applications.
Seamless Robot Integration: Compatible with ABB, KUKA, FANUC, YASKAWA, and other industrial robots.
High-Torque Servo Motor: Delivers smooth, precise motion with ±0.1° repeatability.
Rugged Construction: Reinforced steel frame and corrosion-resistant components for longevity.
Intuitive Programming: User-friendly HMI interface for quick setup and operation.
Safety Compliance: Includes emergency stop, overload protection, and fail-safe mechanisms.
Customizable Fixturing: Modular clamps and adapters for diverse workpiece requirements.
1、Technical parameters: (dimensions and data of the equipment are subject to the digital model and countersigned drawings finally confirmed by both parties)
N/M | Item | Parameters | Remark |
1 | Rated load | 2000kg | Within 650mm radius of axis line |
2 | Rated turning radius | R650mm | |
3 | Rated rotation angle | ±360° | |
4 | Rated rotation speed | 40°/S | |
5 | Repeatability | ≤1.5mm | |
6 | Tail box adjustable stroke | 5000mm | manual adjustment |
7 | Main trunk travel range | 1000-6000mm | |
8 | Dimensions of positioner (length × width × height) | 7000mm×800mm×1350mm | |
9 | Standard turntable | Φ360mm | |
10 | Rotation center height | 1000mm |
Advantages
Enhanced Weld Accuracy: Eliminate misalignment with synchronized head/tail box positioning.
Boost Productivity: Reduce manual adjustments and cycle times by up to 35%.
Cost Efficiency: Minimize scrap, rework, and labor costs through automated precision.
Versatile Applications: Perfect for pipe welding, structural beams, and large-scale fabrication.
Future-Ready Design: Scalable for integration with Industry 4.0 systems and IoT connectivity.
Global Compliance: Meets CE, ISO, and other international industrial standards.