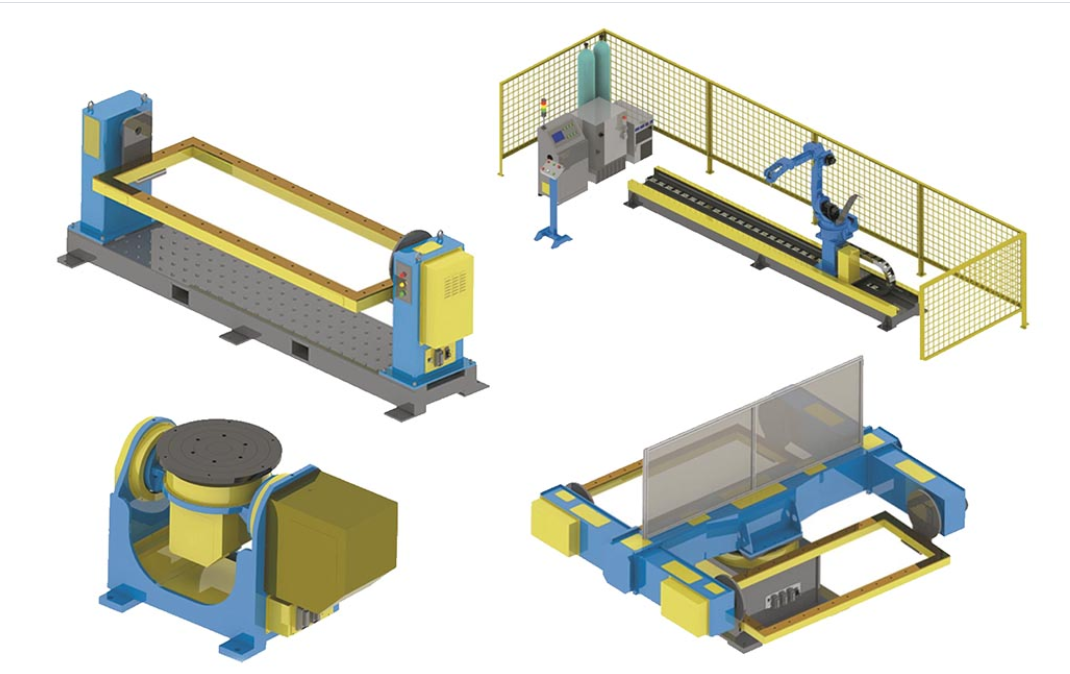


Platform Two-Axis Industrial Robot Servo Welding Positioner – Precision Welding Automation for ABB, KUKA, FANUC Integration
Product Description
The Platform Two-Axis Industrial Robot Servo Welding Positioner is a cutting-edge automation solution engineered to optimize precision, flexibility, and efficiency in robotic welding applications. Designed for seamless integration with ABB, KUKA, FANUC, and other leading robot brands, this positioner enables 360° tilt and 360° rotation for complex welding tasks. Ideal for industries like automotive, aerospace, and heavy machinery, it ensures flawless weld quality while reducing cycle times and labor costs. Built with industrial-grade durability and intuitive controls, it’s the ultimate choice for high-volume production and intricate welding projects.
Structure Briefs: |
This platform two-axis servo positioner is mainly consists of whole welding frame, rotary frame, RV precise reducer, AC servo motor, rotary
support part, conductive system, protective cover and electrical control system.
The whole welding frame is made by high-quality section, the machining was after stress relief annealing, which ensured the machining
accuracy and the use accuracy. Anti-rust appearance paint is beautiful and elegant, and the color can be customized.
Rotary frame is made by high-quality steel section with professional machining. With standard pith tapped hole on the surface for
installing positioning tooling, and it was painted after black oxidation treatment.
The AC servo motor matching the RV reducer can guarantee high rotary stability, high positioning accuracy, long durability and low failure rate.
The conductive mechanism is made in brass, which give perfect conduction. The foundation is whole insulation to protect the servo motor, robot, welding power, etc.
We choose Omron(Japan) PLC to control the positioner and electrical elements are all from famous brand, which ensured the high stability and low failure rate.
Key Features
Dual-Axis Servo Control: Independent tilt (X-axis) and rotation (Y-axis) for precise workpiece positioning.
High Load Capacity: Supports up to 50T for heavy-duty industrial applications.
Seamless Robot Integration: Plug-and-play compatibility with ABB, KUKA, FANUC, YASKAWA, and more.
High-Speed Servo Motors: Delivers rapid, smooth movement with ±0.1° positioning accuracy.
Rugged Construction: Reinforced steel platform and corrosion-resistant components for harsh environments.
User-Friendly HMI: Intuitive touchscreen interface for easy programming and operation.
Safety Compliance: Equipped with emergency stop, overload protection, and fail-safe mechanisms.
Customizable Fixturing: Adaptable clamps and mounts for diverse workpiece geometries.
Technical Specification:
No. | Item | DWP-P-200 | DWP-P-500 | DWP-P-1000 |
1 | Rated load | 200kg (within 2nd axis radius R300mm) | 500kg (within 2nd axis radius R300mm) | 1000kg (within 2nd axis radius R500mm) |
2 | Standard radius of rotary | R400mm | R400mm | R600mm |
3 | rotary angle of 1st axis | ±90° | ±90° | ±90° |
4 | rotary angle of 2nd axis | ±360° | ±360° | ±360° |
5 | Rated rotary speed of 1st axis | 70°/S | 50°/S | 15°/S |
6 | Rated rotary speed of 2nd axis | 70°/S | 70°/S | 24°/S |
7 | Repeated positioning accuracy | ±0.10mm | ±0.12mm | ±0.20mm |
8 | Positioner dimension (L×W×H) | 1000mm×550mm×600mm | 1200mm×600mm×750mm | 1500mm×750mm×900mm |
9 | Standard 2nd axis rotary disc size | φ500mm | φ500mm | φ800mm |
10 | Height of 1st axis rotary center | 500mm | 550mm | 750mm |
11 | Power supply | Three phase 200V ±10% 50Hz (with isolation transformer) | Three phase 200V ±10% 50Hz (with isolation transformer) | Three phase 200V ±10% 50Hz (with isolation transformer) |
12 | Insulation grade | H | H | H |
13 | Weight | about 300kg | about 500kg | about 1000kg |
Advantages
Boost Welding Precision: Eliminate human error with automated, repeatable positioning.
Increase Productivity: Reduce cycle times by up to 40% with synchronized robot workflows.
Cut Operational Costs: Minimize scrap, rework, and manual labor expenses.
Versatile Applications: Perfect for welding, grinding, assembly, and inspection tasks.
Future-Proof Design: Scalable architecture supports upgrades and integration with smart factory systems.